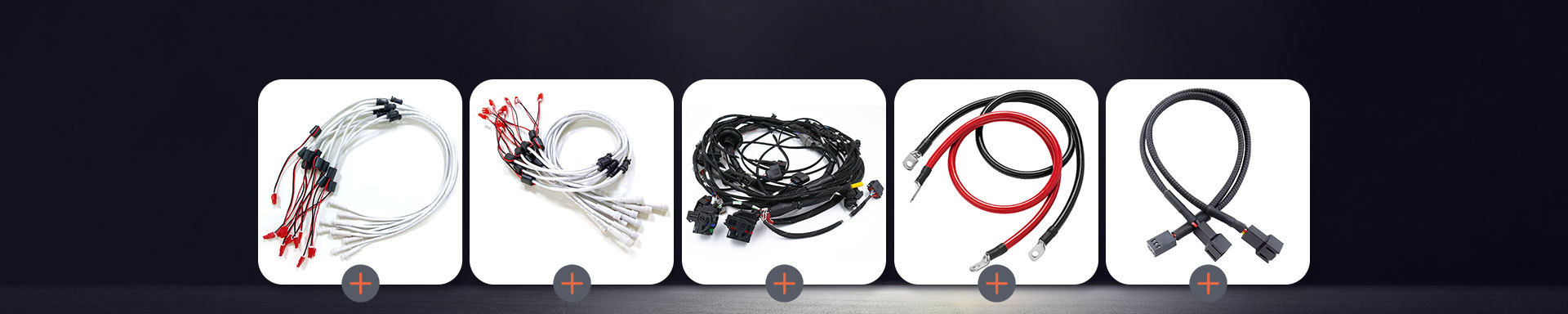
A Beginner’s Guide to Wire Harness Manufacturing
2025-05-19 11:26Wire harness manufacturing, led by a wire harness manufacturer, groups wires and cables into neat bundles. These bundles help move electrical power and signals smoothly, ensuring that devices like home appliances and machines operate effectively. The importance of wire harnesses is highlighted by impressive statistics; in 2025, the global market was valued at $103.59 billion, and by 2034, it is projected to exceed $147 billion, with a consistent growth rate of 4% each year. There are over 830 suppliers in the U.S., including small and women-owned businesses, making this industry crucial to modern technology. Reputable wire harness manufacturers adhere to strict standards, such as ISO 9001, to guarantee safety and quality.
Key Takeaways
Wire harnesses group wires and cables to keep power and signals steady.
Makers follow strict rules like IPC 620 to ensure safety and quality.
The process includes planning, cutting, crimping, putting together, and testing for reliability.
Wire harnesses make things safer, more efficient, and organized in many industries like cars and planes.
New tech like robots and green materials are changing wire harness manufacturing.
Understanding Wire Harness Manufacturing
What is a Wire Harness?
A wire harness is a group of wires, cables, and connectors. It helps carry electrical power and signals in an organized way. You can think of it like the nervous system of a machine or device. It keeps wires neat and safe, so they work properly. Without wire harnesses, wires in cars, appliances, and machines would be messy and might fail.
The wire harness industry follows strict rules to ensure quality. One key rule is the IPC 620 certification. This sets standards for things like crimped connections and soldered ends. It also includes how to label cable assemblies. This certification makes sure products are strong and reliable. It even uses pictures to help manufacturers stay consistent.
Overview of the Manufacturing Process
Making a wire harness involves several important steps. Each step ensures the product is safe and works well. Here’s a simple explanation of the process:
Design and Prototyping: Engineers plan the design based on what the device needs. They choose the right materials and connectors.
Wire Cutting and Stripping: Machines cut wires to the right size and remove insulation from the ends.
Crimping and Soldering: Tools attach connectors to the wires by crimping or soldering.
Assembly: Workers or machines bundle the wires together using ties or sleeves.
Testing and Quality Control: The finished harness is tested to make sure it works and meets standards.
New technology has made these steps faster and better. Robots and cameras now help with wire harness assembly. Robots with special cameras can see and handle parts accurately. This solves problems like finding and tracking parts during tricky tasks.
The rise of electric and smart cars has changed wire harness manufacturing. Car makers now use advanced wire harness technology to make cars safer and better. This shows why knowing the process is important. It affects how reliable modern electrical systems are.
Wire harnesses connect electrical parts in today’s vehicles.
Electric cars are increasing the need for wire harnesses.
People want more advanced car features, boosting this industry.
Rules for safety and fuel efficiency push for better technology.
By learning about these steps and new tools, we see how complex wire harness manufacturing is. It’s not just about bundling wires—it’s about building a strong base for modern technology.
The Importance of Wire Harness Manufacturing
Role in Electrical Systems
Wire harnesses are like the backbone of electrical systems. They help power and signals move smoothly between parts. Without them, cars, appliances, and machines wouldn’t work well. Wire harnesses keep wires neat and safe, stopping damage and making them reliable.
In industries like car manufacturing, wire harnesses are even more important. For example, a 2023 EU rule on recyclable car parts made 68% of EU harness makers update their software. This shows how wire harnesses change to meet new rules. Following certifications like IATF 16949 has also cut delays for electric car parts by 34%. These changes show how wire harnesses keep up with new technology and rules.
Wire harnesses also make vehicles safer. By following ISO 26262 standards, they speed up safety checks for self-driving cars. This ensures cars meet strict safety rules while being made faster. Wire harnesses don’t just connect wires—they help improve safety and innovation in many industries.
Benefits of Wire Harnesses
Wire harnesses have many benefits that make them essential. First, they improve safety. Their strong design lowers the chance of electrical shorts. High-quality materials make them last longer. Bundling wires together stops overheating and electrical fires, making them dependable for important uses.
Another benefit is efficiency. Pre-made harnesses save time during assembly and lower labor costs. They are easier to install and fix, which helps with complex systems. Bundling wires reduces mess and makes routing simpler. This speeds up assembly and makes finding problems easier.
Wire harnesses also keep things organized. Bundled wires look neat and professional. This is important in industries like cars and airplanes, where space is tight, and order matters. Secure connections make them reliable, reducing loose wires and ensuring steady performance.
Here are the main benefits of wire harnesses:
Safer by lowering risks of electrical fires and shorts.
Faster to install, saving time and cutting labor costs.
More organized by reducing mess and making repairs easier.
Reliable with strong connections and durable materials.
Customizable to fit specific needs.
These benefits make wire harnesses key to modern electrical systems. Whether in cars, home devices, or factories, they help everything work safely and smoothly. Knowing these advantages helps manufacturers create top-quality solutions for different industries.
Applications of Wire Harnesses Across Industries
Industries That Use Wire Harnesses
Wire harnesses are important in many fields. They link electrical parts to keep systems running well. Many industries depend on them, such as:
Cars: Wire harnesses act like the nervous system. They connect lights, engines, and safety features.
Airplanes: They power systems that help planes fly safely and efficiently.
Home Devices: Refrigerators and washing machines need wire harnesses to work daily.
Factories and Hospitals: Machines and medical tools use them for accuracy and dependability.
Green Energy: Solar panels and wind turbines rely on them to move power.
These examples show how flexible wire harnesses are. They can fit many needs, making them very useful.
Real-Life Uses of Wire Harnesses
Wire harnesses are used in many real-world ways. In construction, they power elevators, escalators, and lights. More building projects have increased their demand. Electric and hybrid cars also need special harnesses for power and connections.
In airplanes, lightweight harnesses save fuel and improve performance. Telecom companies use them for fast data transfer. Eco-friendly trends have also changed harness designs. Companies now use materials that are better for the planet.
Wire harnesses grow smarter with new technology. They now help share data and improve how industries work. Keeping up with these changes helps manufacturers meet the needs of different fields.
The Wire Harness Manufacturing Process
Key Steps in Manufacturing
Making a wire harness involves clear steps to ensure it works well. Each step builds on the one before it. Here’s a simple breakdown:
Material Preparation: First, gather wires, connectors, and insulation. These parts are chosen to match the design.
Wire Cutting and Preparation: Machines cut wires to the right size. Ends are stripped, and labels are added for easy tracking.
Crimping and Termination: Wires are joined to connectors using crimping tools. This step makes sure the connections are strong.
Assembly: Workers or machines group the wires together. They use ties or sleeves to keep them neat and follow the design plan.
Testing: The finished harness is tested to check safety and function. This ensures it meets industry rules.
Each step is important for making a good wire harness. By following these steps, manufacturers create reliable products for many industries.
Quality Control and Testing Standards
Quality checks are very important in wire harness making. They make sure every product is safe and works well. Manufacturers use these methods to keep quality high:
Following rules like ISO 9001 and IPC/WHMA-A-620 ensures safety and performance.
Prototyping and testing check if the harness is strong and works in tough conditions.
Random checks confirm the process follows the rules.
First-off tests check the first product to ensure the process is correct.
Visual tools, like diagrams and instructions, help workers during assembly. These tools reduce mistakes and keep things consistent. The table below shows key quality steps:
By using these quality checks, manufacturers make wire harnesses that are safe, strong, and dependable.
Challenges and Innovations in Wire Harness Manufacturing
Common Challenges in the Industry
Wire harness manufacturing has many challenges that affect progress. Managing inventory is one big problem. Manufacturers handle different product setups, making stock control hard. Poor inventory tracking can cause stockouts, losing up to 20% in sales. Too much inventory raises storage costs, hurting profits.
Getting materials from global suppliers is another issue. While it can save money, it also brings risks. Political problems and trade changes, like Brexit, make supply chains tricky. Following strict safety rules adds more difficulty. It needs lots of paperwork and testing, which slows production and increases wait times.
Sustainability is becoming more important too. Companies must use eco-friendly methods while staying profitable. This means finding new suppliers and using greener materials. Adding advanced tools, like tracking software, also costs money and needs training. It can disrupt work for a while but helps in the long run.
In aerospace, wire harness assembly is especially complex. Thousands of wires and connectors must be put together carefully. To solve this, companies like Boeing use smart glasses and tools like Skylight. These cut production time by 25%, showing how the industry tackles challenges.
Emerging Trends and Technologies
The wire harness industry is changing fast with new ideas and tools. One exciting update is advanced design software. Programs like Harness Builder 2023 by Zuken Inc. make designing easier and faster.
Lightweight and strong materials are also becoming popular. These improve fuel use in cars and planes. High-strength composites and light metals are now common in making harnesses. Automation and artificial intelligence (AI) are also improving production. Machines and AI designs make work quicker and more reliable.
Eco-friendly practices are another focus. Manufacturers are using greener materials and methods to help the planet. This matches the growing need for sustainable solutions in industries.
Key Trends in Wire Harness Manufacturing:
Lightweight materials improve fuel use in vehicles and planes.
Automation and AI make production faster and better.
Eco-friendly methods reduce harm to the environment.
Strong composites and advanced metals boost performance.
These updates are shaping the future of wire harness manufacturing. By using these trends, manufacturers can solve problems and meet modern needs.
The Role of a Trusted Wire Harness Manufacturer
Why Choose Xiamen Evershine Electronic Technology?
Picking the right wire harness maker is important. At Xiamen Evershine Electronic Technology, we focus on quality and meeting your needs. We know every industry is different. That’s why we create custom designs that follow strict rules like ISO 9001 and IPC/WHMA-A-620. These rules make sure our products are safe and meet important standards, especially for medical devices.
We also make sure our products work in tough conditions. For industries like aerospace and defense, wire harnesses must handle stress. Our custom designs stay reliable even in harsh environments. This builds trust and strong partnerships with our clients.
To keep quality high, we use advanced tests. For example:
These tests make sure our products are safe and long-lasting.
Commitment to Quality and Innovation
At Xiamen Evershine Electronic Technology, we focus on both quality and new ideas. We check quality at every step of making wire harnesses. From picking materials to final testing, we make sure everything works well. Visual checks and early tests help us fix problems quickly. This keeps our products consistent and reliable.
We also use new tools and ideas to improve. Automation and AI help us work faster and more accurately. We use lightweight materials and eco-friendly methods in our designs. These changes make our products better and help the environment.
By focusing on quality and new ideas, we make products that go beyond expectations. Whether you need a simple or complex design, we’re ready to help. As a trusted wire harness maker, we’re here to support the future of technology.
Wire harness manufacturing is key to powering modern electrical systems. It helps send power and data smoothly in many industries. These include cars, planes, and factories. The table below shows why wire harnesses are important:
Xiamen Evershine Electronic Technology is proud to make trusted wire harnesses. We focus on quality and new ideas to meet industry needs. Choosing us means working with a partner who helps improve modern technology.
FAQ
What’s the difference between a wire harness and a cable assembly?
A wire harness groups wires into one bundle. A cable assembly connects cables with parts like plugs. Wire harnesses keep wires tidy, while cable assemblies focus on linking components.
How long does it take to make a wire harness?
The time depends on how complex the design is. Simple ones take hours, but detailed ones for planes may take days. Automation tools can make the process faster.
Can wire harnesses be made for special needs?
Yes, wire harnesses can be customized for different uses. They can have specific lengths, connectors, and materials for cars, medical tools, and more.
Why is quality control important in wire harness making?
Quality checks make sure harnesses are safe and work well. Following rules like ISO 9001 and IPC/WHMA-A-620 prevents problems and ensures they last longer.
Are wire harnesses good for the environment?
Many companies now use eco-friendly materials and methods. These greener practices help reduce waste and meet environmental rules.