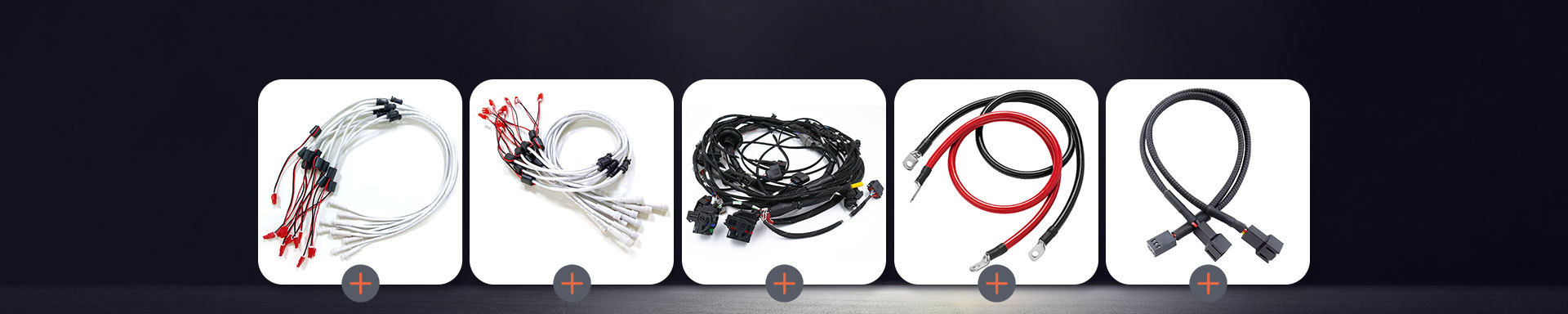
5 Key Factors for Selecting the Best Power Cord Supplier in China
2025-08-10 14:585 Key Factors for Selecting the Best Power Cord Supplier in China
When you want to find a reliable power cord supplier in China, remember these five important things:
Certifications
Quality control
Technical compliance
Reputation
Customization, pricing, and support
Certifications are crucial because they protect you from danger and legal issues. Many major markets, such as North America and Europe, have very strict regulations. If you don’t comply with these rules, you could face hefty fines, product recalls, or even legal action. Using this checklist will help your business stay safe and succeed when working with a reliable power cord supplier.
Key Takeaways
Always look for important certifications like VDE, UL, CE, SAA, and the China Compulsory Certificate. These show the power cord is safe and follows the law.
Check the supplier’s quality control by doing factory checks, testing samples, and reading inspection reports. This helps you avoid bad or unsafe power cords.
Make sure the power cord’s technical details, like voltage, current, plug type, and wire gauge, match your device and the market you want to sell in.
Pick suppliers with a good name, lots of experience, and good reviews. This helps you get products on time and with good quality.
Find suppliers who let you customize, give clear prices, and have strong after-sales help. This will help your business needs.
Ask for full certificates, test results, and technical data sheets. This proves what the supplier says and helps you avoid mistakes that cost money.
Talk about the smallest order you can make and ask about OEM or ODM services. This gives you more choices that fit your budget and product plans.
Keep talking with your supplier. This helps you get fast help, technical advice, and makes orders go smoothly.
Certifications
When you look for a power cord supplier in China, certifications should be at the top of your checklist. Certifications show that a supplier takes safety and quality seriously. They also help you avoid trouble with customs or product recalls.
International Standards
VDE, UL, CE, SAA, etc.
You want your power cords to work safely in every country where you sell your products. That means you need to check for international certifications. Here are some of the most important ones:
VDE: This is a must for Europe. It proves the cords meet strict German and European safety rules.
UL: If you plan to sell in the United States, look for UL certification. It shows the cords pass tough American safety tests.
CE: This mark is needed for the European Union. It means the product meets EU safety, health, and environmental standards.
SAA: For Australia and New Zealand, SAA approval is key.
A good supplier will have these certificates ready to show you. If they hesitate or make excuses, that’s a red flag.
CCC Mark
The China Compulsory Certificate (CCC) is the main local certification. Every power cord made or sold in China must have this mark. The CCC mark proves the product passed strict tests and meets Chinese safety laws. Chinese manufacturers usually have a very high pass rate—about 99.9%—when it comes to these local checks. They also often hold international certifications like ISO9001 and CE, so you get both local and global quality.
Compliance
Target Market Regulations
You need to match the certifications to your target market. For example, if you sell in Europe, you need VDE and CE. For the US, you need UL. Each country has its own rules. If you skip this step, your products might get stuck at customs or even banned from sale.
Tip: Always ask your supplier for copies of their certificates. Double-check the details, like the certificate number and expiration date, to make sure they are real.
Industry-Specific Needs
Some industries have extra rules. Medical devices, for example, need special safety marks. If you work in a field with strict standards, tell your supplier right away. They should know what you need and help you get the right certifications.
Certifications do more than just tick a box. They protect your business and your customers. When you choose a supplier with the right certifications, you lower your risk and build trust with buyers.
2. Quality Control
When you pick a power cord supplier, you want every cord to be safe. Quality control is very important for any good supplier. If a supplier skips steps, cords might break or overheat. Bad cords can even cause fires. Here is what you should check.
Inspection
Factory Audits
You should ask about factory audits. These audits check if the factory follows rules for making power cords. Auditors look at how workers use materials and how machines work. They also check if the factory keeps records and follows safety rules. Audits use attribute sampling. This means inspectors pick random cords from a batch to check for problems. This method helps you know the quality of the whole batch. Most audits use a 95% confidence level. This means you can trust the results.
Sample Testing
Sample testing is another big part of quality control. Suppliers do not check every cord. They use smart sampling to save time and money. Here are some ways they do it:
Simple Random Sampling: Every cord can be picked.
Stratified Sampling: The batch is split into groups, and samples come from each group.
Cluster Sampling: Inspectors pick whole groups at random.
Acceptance Sampling (AQL): Inspectors use set rules to decide if a batch passes or fails.
You should know about the tests used on power cords:
Power Cord Strain Relief Test: Checks if the cord can handle pulling and bending.
Earth Continuity Test: Makes sure the cord will not shock you.
Electric Strength Test: Tests if the cord can handle high voltage.
Battery Reverse Voltage Test: Checks if the cord stays safe if the battery is put in wrong.
Many suppliers use AI and machine vision to find problems faster. Some even let you do remote inspections, so you can check quality from far away.
Manufacturing
Material Sourcing
Ask your supplier where they get their materials. Good suppliers use high-quality copper, strong insulation, and safe plugs. They check every shipment before making cords. Pre-Production Inspection (PPI) helps catch problems early. This way, bad materials do not get used.
Consistency
Consistency is very important. You want every cord to be made the same way. Suppliers use During Production Inspection (DPI) to check cords as they are made. They also do Pre-Shipment Inspection (PSI) to make sure finished cords are safe before shipping. Some even watch the loading process to stop damage during shipping. Suppliers use tools like the chi-square test to find patterns in defects and fix problems fast.
Tip: Always ask for inspection reports and test results. A supplier who shares this info is more likely to give you safe, high-quality cords every time.
If you follow these quality control steps, you lower your risk of getting bad cords. You also keep your business and your customers safe.
3. Technical Compliance
When you choose a power cord supplier, you need to make sure every cord matches your device’s technical needs. If you skip this step, you might end up with cords that don’t fit, overheat, or even cause damage. Let’s break down what you should look for.
Specifications
Voltage and Current
First, check the voltage and current ratings. Every device has its own requirements. If you use a cord with the wrong rating, it can overheat or fail. The IEC 60320 standard helps you match the right cord to your device. For example, some cords work up to 250 volts and 16 amperes. Others handle less. The standard also covers temperature ratings, so you know if a cord can handle heat from your device.
Here’s a quick look at common connector types and their ratings:
Tip: Always check the label on your device and compare it to the cord’s specs. If you’re not sure, ask your supplier for a chart or technical sheet.
Plug Types
Plug types matter a lot. Different countries use different plugs. For example, the US uses NEMA 5-15P, while Europe uses CEE 7/7 or BS 1363. If you pick the wrong plug, your cord won’t fit the outlet. Suppliers should offer a range of plug types and help you choose the right one for your market.
Wire Gauge (AWG)
Wire gauge tells you how thick the wire is. Thicker wires (lower AWG numbers) carry more current. Here’s a quick guide:
Lower AWG = thicker wire = more power. Always match the wire gauge to your device’s needs.
Application Fit
Industry Requirements
Some industries have special rules. Medical, industrial, and IT equipment often need cords with extra safety features or certifications. If you work in these fields, tell your supplier exactly what you need. They should know the standards for your industry and help you pick the right cords.
Manufacturer Data
Suppliers should give you technical data sheets and charts. These documents show voltage, current, plug type, wire gauge, and insulation details. Use these to double-check that every cord matches your device. If a supplier can’t provide this info, it’s a warning sign.
Note: Always ask for technical data before you order. This helps you avoid costly mistakes and keeps your devices safe.
4. Reputation of Reliable Power Cord Supplier
Reputation is very important when picking a power cord supplier. It is just as important as certifications or technical details. A good reputation means the supplier keeps promises and makes customers happy. If you ignore this, you could get late orders or unsafe cords.
Track Record
Years in Business
You should choose a supplier with lots of experience. If a company has been around for many years, it knows how to solve problems. Older companies usually have better ways to check quality and help customers. Ask, “How long have you made power cords?” If they say five years or more, that is a good sign.
Major Clients
Big brands only work with suppliers they trust. If you see names like Belkin or Tripp Lite, you know the supplier is good. These brands care about safety and want reliable cords. Suppliers with global clients know many rules and needs. Here are things that show a supplier is strong:
Orders arrive on time most of the time
Few cords are returned or have problems
You know when your order will come
The company is not likely to close soon
Most customers are happy with the service
Tip: Ask for a list of big clients. Check if the supplier has worked with companies near you.
Reviews
Third-Party Ratings
You can learn a lot from ratings on websites. Sites like Alibaba or Made-in-China show scores and badges. Pick suppliers with high scores and good comments. Some sites show how often orders are on time. These numbers help you find a supplier you can trust.
Online Feedback
You should also read online reviews. Search for the supplier’s name and see what buyers say. Look for comments about quality and delivery. If many people complain about the same thing, be careful. If most reviews are good, you can feel safer.
A good power cord supplier has a strong history and happy customers. Checking these things helps you avoid problems and keeps your business safe.
5. Customization, Pricing, and Support
When you look for a power cord supplier, you want more than just good products. You need a partner who can meet your needs, offer fair prices, and help you after the sale. Let’s break down what to check.
Customization
Every business is different. You may need cords in special colors, lengths, or with unique connectors. A flexible supplier can help you stand out in your market.
MoQs
Minimum Order Quantities (MOQs) show how flexible a supplier is. Some suppliers want you to buy large batches. Others let you start small. Here’s what you can do to get the best deal:
Ask why the MOQ is set at that number. Sometimes it’s because of their subcontractors or the materials they use.
Try to use standard parts. This can lower the MOQ.
Offer to pay a bit more if you want a smaller order.
Use the same parts across your products. This helps you meet the MOQ faster.
Negotiate directly with the supplier. Many will work with you if you ask.
A supplier with low or flexible MOQs makes it easier for you to test new products or enter new markets.
OEM/ODM
You might see the terms OEM and ODM. Here’s what they mean:
OEM (Original Equipment Manufacturer): You give the design, and they make it. This is good if you know exactly what you want.
ODM (Original Design Manufacturer): They design and make the product for you. This is great if you want new ideas or need help with design.
CDMO (Contract Development and Manufacturing Organization): They do everything—design, materials, and even help with rules and laws.
Suppliers who offer ODM or CDMO services can give you more choices and help you create products that fit your brand.
Customization helps you meet customer needs and keeps your business ahead of the competition. Many companies now use digital tools and AI to speed up custom orders and improve quality.
Pricing
You want clear and fair prices. Hidden fees can hurt your profits.
Transparency
A good supplier tells you exactly what you are paying for. They give you a full quote with no surprises.
Cost Breakdown
Ask for a cost breakdown. This should show:
Material costs
Labor costs
Packaging
Shipping
When you see all the details, you can compare suppliers and pick the best value.
After-Sales Support
Support does not end when you get your order. You need help if something goes wrong.
Technical Help
A strong supplier offers technical support. They answer your questions about installation, safety, or repairs.
Communication
Good communication makes everything easier. Look for suppliers who reply quickly and clearly. They should have staff who speak your language and understand your needs.
Tip: Compare offers from different suppliers. Make sure you can reach them easily by phone, email, or chat.
Choosing a supplier with flexible customization, clear pricing, and strong support helps your business grow and keeps your customers happy.
When picking a good power cord supplier in China, follow this checklist:
Look at certifications, quality checks, technical rules, reputation, and support.
Certifications and quality checks help stop problems and unhappy customers.
A good reputation and clear talks help you avoid supply troubles.
Using facts to compare helps you find risks, save money, and plan for the future.
Then, compare suppliers, check their history, and plan visits to their factories for extra safety.
Choosing the right supplier keeps your business safe, strong, and ready to grow.
FAQ
What certifications should I ask for when buying power cords from China?
You should look for VDE, UL, CE, SAA, and the CCC mark. These show the cords meet safety rules in different countries. Always ask your supplier for copies of these certificates.
How can I check if a supplier is reliable?
Check their years in business and see if they work with big brands. Read online reviews and ratings. You can also ask for references from other customers.
Why does wire gauge matter for power cords?
Wire gauge tells you how much current the cord can handle. Thicker wires (lower AWG numbers) carry more power. Using the wrong gauge can cause overheating or even fires.
Can I order custom power cords with my own logo?
Yes! Many suppliers offer OEM and ODM services. You can ask for special colors, lengths, or your own logo. Just tell the supplier what you need.
What is the usual minimum order quantity (MOQ) for power cords?
MOQs can be as low as 100 pieces, but some suppliers want bigger orders. You can try to negotiate. Using standard parts or paying a bit more may help lower the MOQ.
How do I know if the power cords will fit my country’s outlets?
Ask your supplier for the right plug type for your country. You can also send them a photo of your outlet. They should help you pick the correct plug.
What should I do if I get faulty power cords?
Contact your supplier right away. Good suppliers offer after-sales support and will replace or refund faulty cords. Always keep records and photos of any problems.
How long does it take to get power cords shipped from China?
Shipping times depend on your location and the shipping method. Air shipping takes about 5–10 days. Sea shipping can take 20–40 days. Ask your supplier for a tracking number.